Optimizing Your Welding WPS: Methods for Improved Performance and Effectiveness
Optimizing Your Welding WPS: Methods for Improved Performance and Effectiveness
Blog Article
Mastering Welding WPS Specifications: Ideal Practices and Techniques for High Quality Welds
In the realm of welding, understanding Welding Treatment Requirements (WPS) standards is a vital element that straight affects the top quality and stability of welds. As we browse via the complexities of welding WPS criteria, revealing key insights and approaches for attaining top-tier welds will be extremely important for welders looking for to stand out in their craft and produce welds that stand the examination of time.
Recognizing Welding WPS Criteria
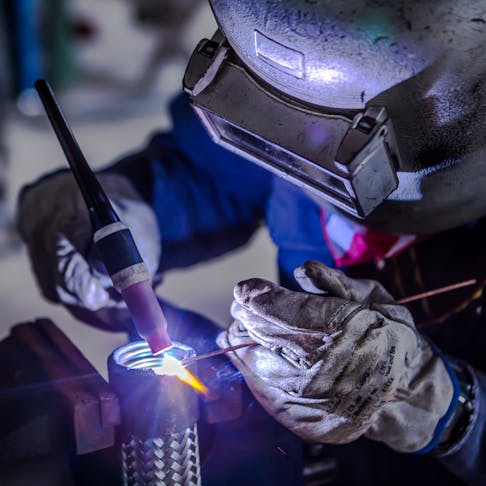
Examiners rely on WPS documentation to confirm that welding treatments are being followed correctly and that the resulting welds are of high quality. Designers use WPS criteria to develop welding procedures that make certain the durability and integrity of welded structures.
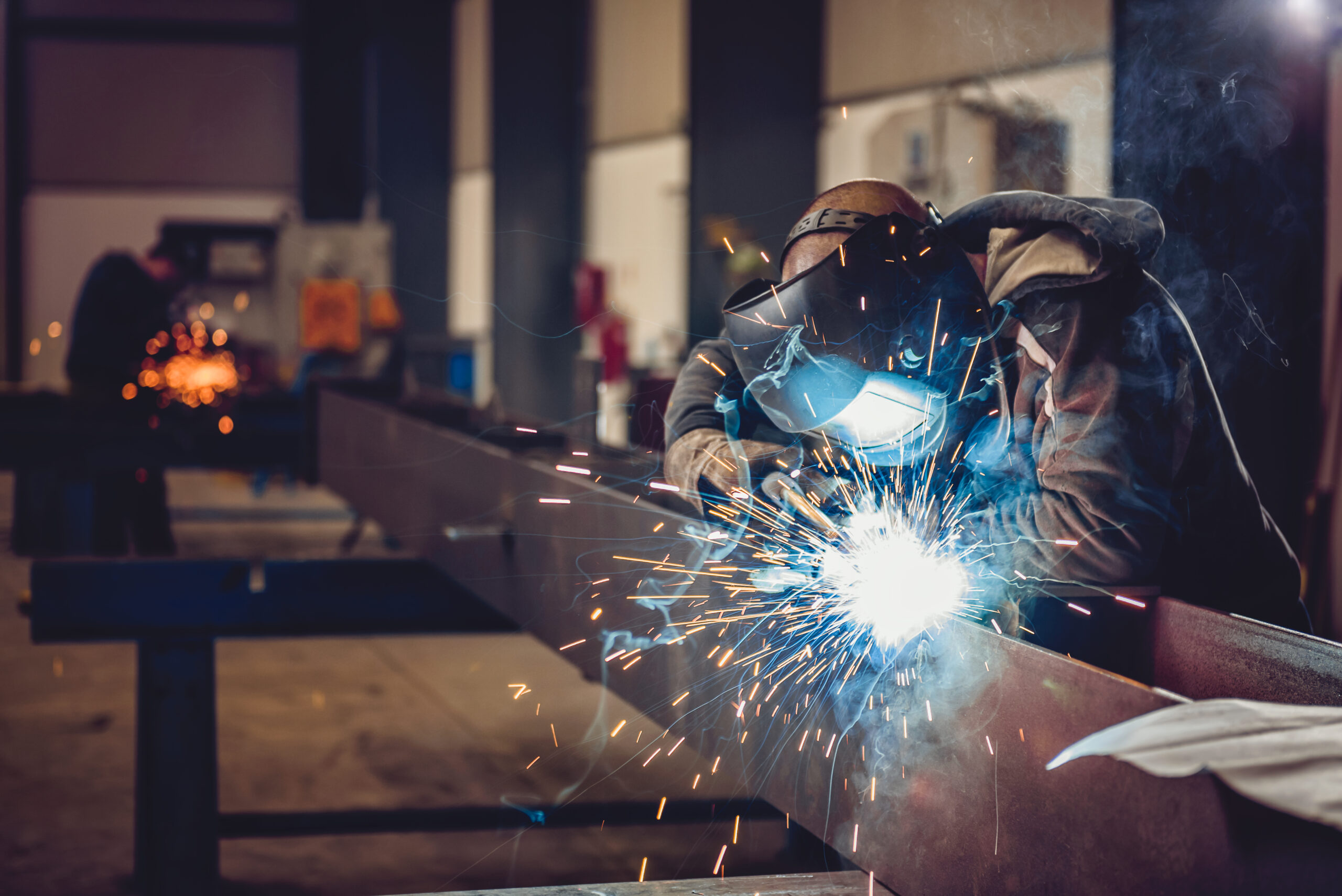

Necessary Tools for Quality Welds
Mastering welding WPS criteria is crucial for welders to effectively make use of the vital devices required for producing high quality welds. The type of welding equipment required depends on the welding procedure being utilized, such as MIG, TIG, or stick welding. Wire brushes and chipping hammers are essential for cleansing the weld joint before and after welding to get rid of any type of contaminations that might impact the top quality of the weld.
Key Techniques for Welding Success
To accomplish welding success, one need to grasp the key strategies necessary for creating high-quality welds. One vital method is preserving the appropriate arc length. Maintaining the electrode at the ideal range from the work surface is crucial for producing solid, consistent welds. In addition, managing the travel speed is extremely important. Moving also swiftly can cause not enough penetration, while relocating also gradually can cause too much warmth input and possible problems. Appropriate manipulation of the electrode angle is one more crucial strategy. The angle at which the electrode is held can affect the grain form and penetration of the weld. Moreover, guaranteeing consistent gun angle and direction of traveling is crucial for uniformity in the weld grain. Lastly, keeping a secure welding and a steady hand position throughout the procedure is vital to achieving precision and consistency in the welds. By grasping these crucial strategies, welders can elevate the quality of their job and achieve welding success.
Ensuring Conformity With WPS Standards
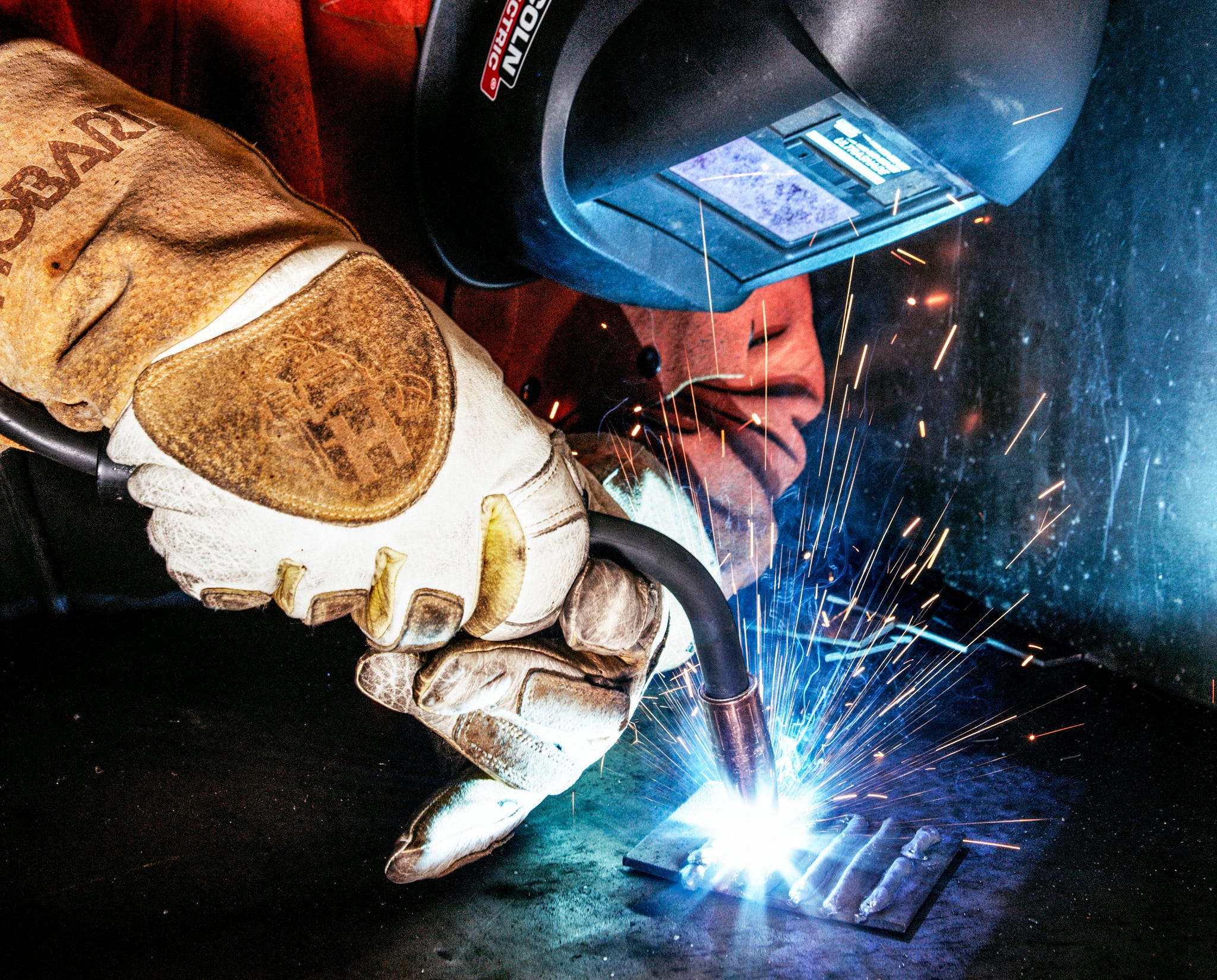
Furthermore, welders need to click here for more info undergo training to familiarize themselves with the WPS standards pertinent to their job. Normal audits and examinations should be performed to confirm that welding activities align with the suggested WPS guidelines. Furthermore, maintaining comprehensive documents of welding criteria, equipment calibration, and examination outcomes is important for demonstrating conformity with WPS criteria - welding WPS. By diligently sticking to WPS standards, welders can make certain that their work satisfies the needed quality levels and contributes to the total success of the welding job.
Troubleshooting Common Welding Issues
When encountered with usual her comment is here welding problems, determining the root cause is important for efficient troubleshooting. One common issue is the visibility of porosity in welds, typically brought on by contaminants such as wetness, oil, or rust. To resolve this, guaranteeing correct cleaning of the base metal before welding and making use of the right protecting gas can significantly lower porosity. Another concern regularly experienced is absence of fusion, where the weld falls short to appropriately bond with the base material. This can come from insufficient warm input or improper welding technique. Changing parameters such as voltage, cord feed rate, or take a trip speed can help enhance combination. Furthermore, distortion, fracturing, and spatter prevail welding challenges that can be reduced through appropriate joint prep work, consistent warmth control, and selecting the ideal welding consumables. By completely recognizing these typical welding problems and their origin triggers, welders can efficiently fix issues and accomplish high-quality welds.
Conclusion
To conclude, mastering welding WPS standards calls for a thorough understanding of the standards, utilizing crucial tools, and carrying out crucial strategies for successful welds. Ensuring conformity with WPS requirements is important for creating top quality welds and avoiding usual welding problems. By complying with best methods and techniques, welders can attain consistent and reliable lead to their welding projects.
In the realm of welding, understanding Welding Treatment my latest blog post Specification (WPS) criteria is an essential element that straight influences the top quality and stability of welds.When diving into the world of welding techniques, a crucial element to comprehend is the importance and complexities of Welding Procedure Requirements (WPS) requirements. WPS requirements provide an in-depth standard for welding operations, making certain consistency, quality, and safety in the welding process. The kind of welding maker required depends on the welding process being used, such as MIG, TIG, or stick welding.Accomplishing welding success with the proficiency of crucial methods requires a complete understanding and adherence to Welding Treatment Specification (WPS) criteria.
Report this page